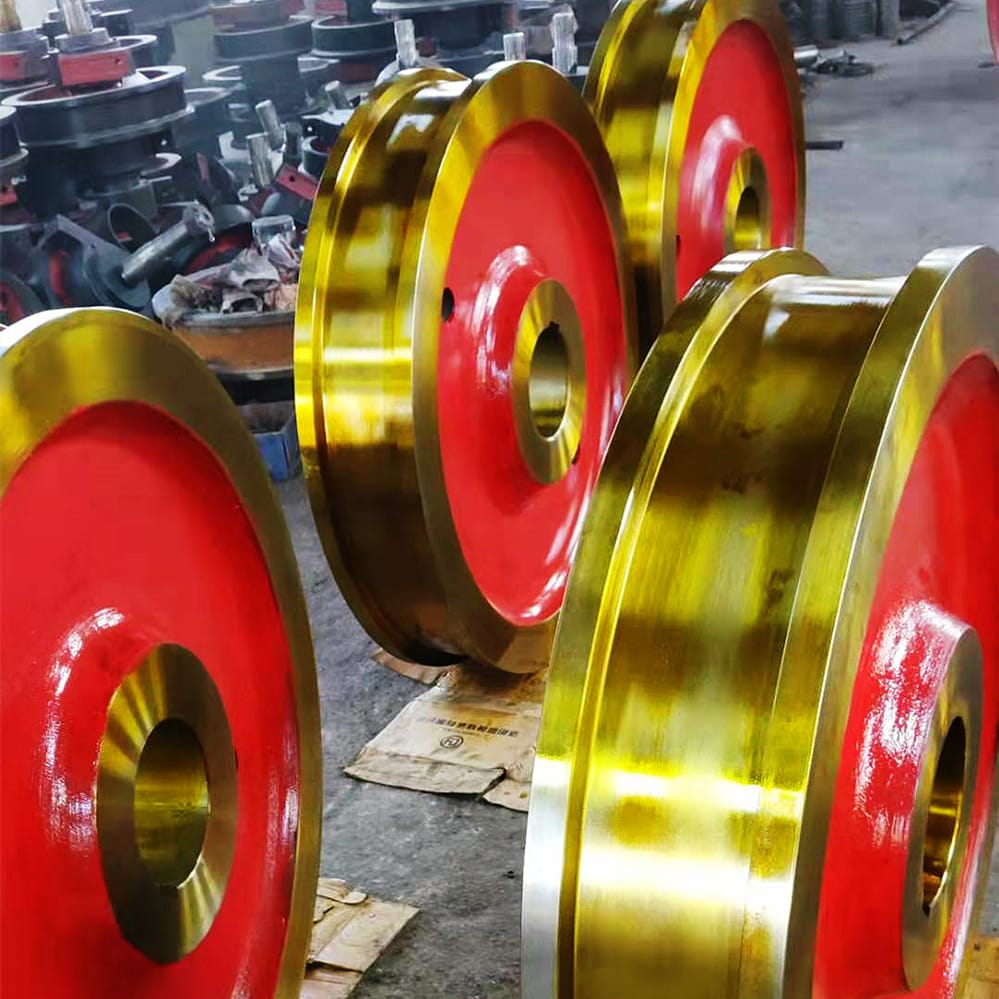
Parameter | Range |
Load Capacity | 500kg-120 Tons |
Weight | 50-800kg/pcs |
Wheel Diameter | 400 mm to 1200 mm, customizable |
Wheel Width | 200 mm to 500 mm,customizable |
Operating Temperature | -20°C to 60°C |
Material | High-strength Steel |
Control Type | Manual, Remote, or Automatic |
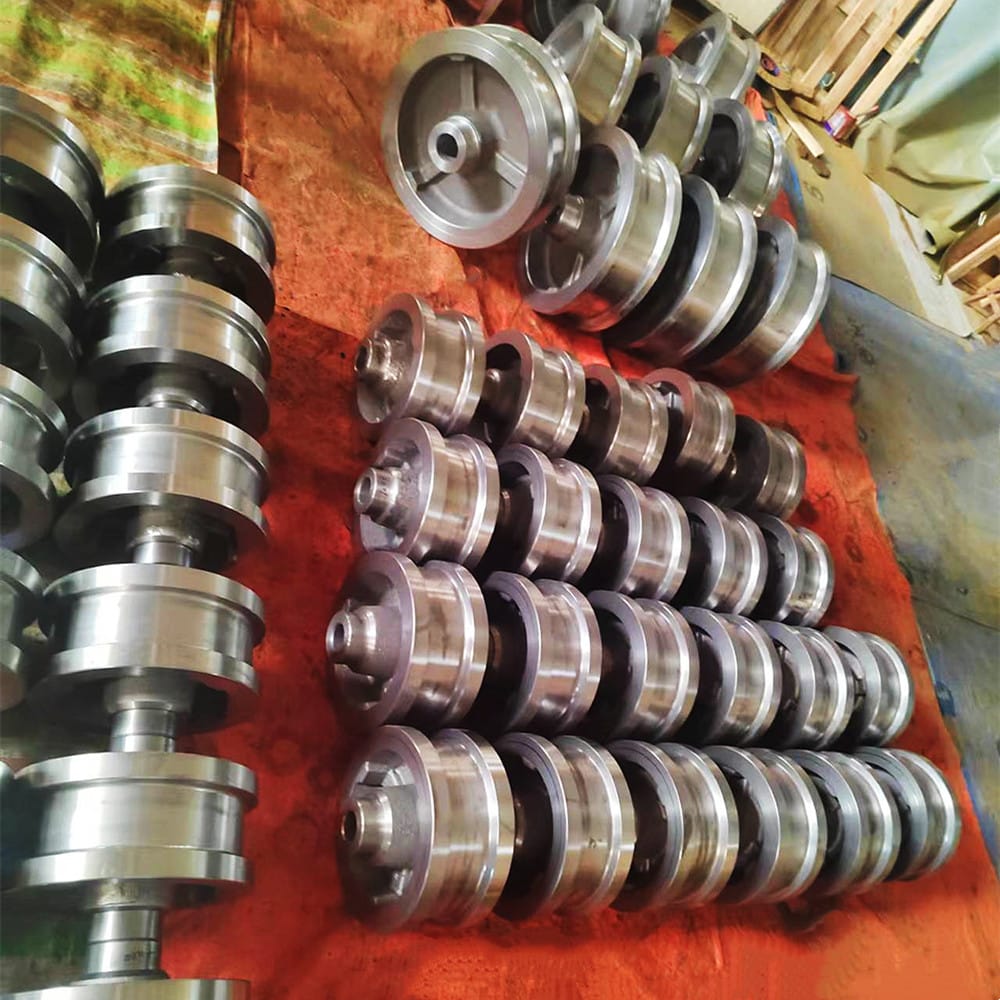
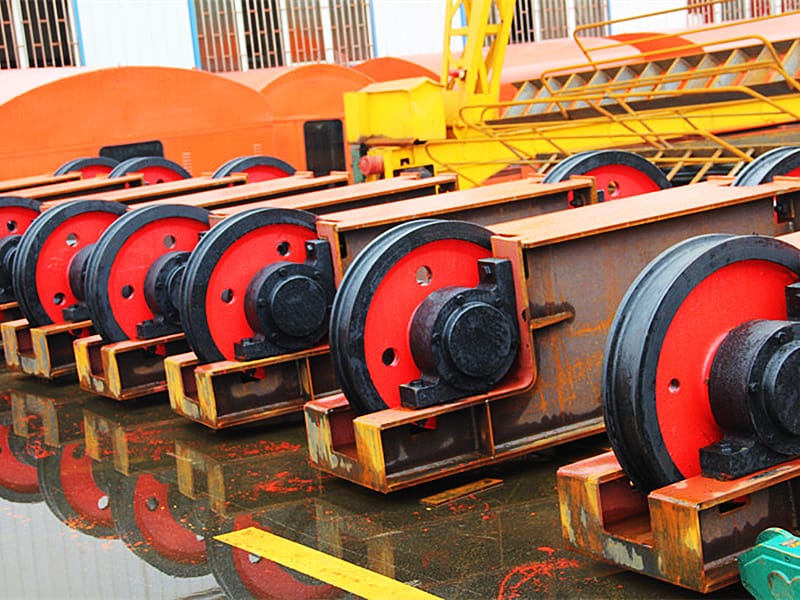
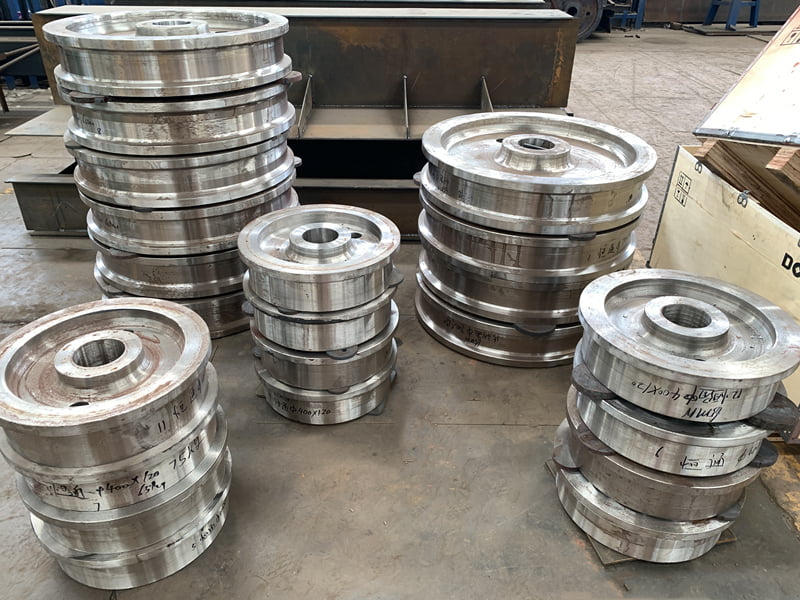
Crane Wheel: The Backbone of Heavy Lifting
What is a Crane Wheel?
At its core, a crane wheel is a crucial component of crane machinery(both overhead cranes and gantry cranes) that allows for the movement of loads across different surfaces. Without these wheels, a crane simply wouldn’t be able to perform its primary function: moving massive, heavy loads safely and efficiently. Whether it’s an overhead crane in a warehouse or a gantry crane at a shipyard, the wheels take on the weight and strain that would otherwise be impossible to manage
The Importance of Crane Wheels in Industrial Machinery
Crane wheels might not be the flashiest part of the crane, but they are integral to its function. Think about it: without smooth, sturdy wheels, your crane wouldn’t be able to glide smoothly along tracks or handle heavy materials efficiently. They directly affect how well the crane performs and how long it lasts. Not to mention, they play a key role in keeping operations safe and running smoothly. Let’s dive a little deeper into why they’re so important.
Why Crane Wheels Matter for Safety
Safety is always the top priority when dealing with heavy machinery. A crane that’s hard to control or unstable can quickly become a hazard. The wheels are often the first point of failure if they’re not in good condition. Damaged or worn-out crane wheels can lead to accidents, and regular inspection is essential to catch any issues before they become dangerous. By choosing the right type of wheel and keeping it well-maintained, you significantly reduce the risks associated with crane operation.
The Role of Crane Wheels in Productivity
Productivity is another reason crane wheels matter. When they’re functioning properly, crane operations are smoother and faster. That means fewer interruptions, more uptime, and increased productivity. Damaged wheels slow down the operation, costing time and money. So, investing in high-quality crane wheels pays off in the long run by keeping operations moving efficiently.
Different Types of Crane Wheels
Not all crane wheels are the same! In fact, there are several different types designed for specific needs and environments. Knowing which type of wheel to use can make a significant difference in performance and longevity. Let’s take a look at some of the most common types you’ll come across.
Single Flange vs. Double Flange Wheels
Single flange wheels have one raised edge, which helps guide them along a track. Double flange wheels, as the name suggests, have two raised edges for added stability, especially when moving on rougher surfaces or in applications where precise guidance is critical. Both types are widely used, but the choice between them depends on the specific demands of your crane’s tasks.
V-Groove Crane Wheels
V-groove crane wheels are designed to operate on inverted angle iron tracks, which provides better guidance and prevents the wheel from slipping off the track. These are often used in smaller crane systems where maneuverability and precision are essential.
Tapered Tread Crane Wheels
Tapered tread wheels feature a slight angle that helps distribute the load evenly across the wheel’s surface. This design minimizes wear and tear and prolongs the wheel’s lifespan. It’s especially beneficial for high-capacity cranes that frequently handle heavy loads.
Materials Used in Crane Wheels
The material a crane wheel is made from plays a huge role in how it performs. Different materials offer different strengths, wear resistance, and durability. So, what are the most common materials used in crane wheels, and what makes each one unique?
Steel Crane Wheels
Steel is by far the most common material for crane wheels. It’s strong, durable, and highly resistant to wear and tear. Steel wheels are ideal for heavy-duty applications where cranes are constantly moving large, heavy loads. The downside is that they can be a bit noisy and may require regular lubrication to keep friction in check.
Cast Iron vs. Ductile Iron Wheels
While steel is common, cast iron and ductile iron are also frequently used in crane wheel manufacturing. Cast iron is cheaper but more brittle, making it better for light-duty applications. Ductile iron, on the other hand, combines the strength of steel with the affordability of cast iron, offering a middle-ground solution.
Key Considerations When Choosing Crane Wheels and DRS Wheel Blocks
Choosing the right crane wheels isn’t just about picking what’s available. You need to consider several factors to ensure you’re getting the most out of your investment. Here’s what to keep in mind:
Load Capacity
First and foremost, how much weight will your crane be moving? The load capacity of the wheel needs to align with the crane’s maximum weight limits. Using undersized wheels can lead to serious wear and potential failures.
Environmental Conditions
Will your crane be operating indoors or outdoors? In hot, cold, or wet environments? Different environmental conditions can impact the material and type of wheel you choose. For instance, steel wheels might rust if used in a highly humid environment unless they’re treated or coated for protection.
Wheel Design and Durability
The design of the wheel, including the tread and flanges, will influence how long it lasts and how well it performs. Durability is especially important in high-use industrial environments, where crane wheels are expected to last for years with minimal downtime.
The Manufacturing Process of Crane Wheels
Ever wonder how these essential components are made? The manufacturing process has a lot to do with the performance and durability of crane wheels. Here’s a look at the most common methods:
Forging vs. Casting
Forging involves heating metal and then shaping it under high pressure, resulting in a stronger, more durable product. Casting, on the other hand, involves pouring molten metal into a mold. While casting is faster and cheaper, forged wheels are generally more durable and better suited for heavy-duty applications.
Heat Treatment for Enhanced Durability
After forging or casting, many crane wheels undergo heat treatment. This process strengthens the metal and enhances its wear resistance, ensuring the wheels can handle the demands of heavy lifting.
Common Issues with Crane Wheels and How to Solve Them
Despite their durability, crane wheels can still encounter problems. Here are some of the most common issues and how to fix them:
Wear and Tear
Like any moving part, crane wheels wear down over time. Regular inspection and timely replacement are key to avoiding major problems. If you notice uneven wear, it could be a sign of misalignment or improper load distribution.
Misalignment
Misaligned wheels can cause uneven wear and affect the crane’s performance. This issue is often fixed by adjusting the crane’s track or realigning the wheels to ensure smooth operation.
Overloading
Pushing a crane beyond its weight limits can put excessive strain on the wheels. Regularly check load capacities and avoid overloading the crane to prolong wheel life.
Crane Wheel Maintenance and Inspection
Regular maintenance is essential to keep your crane wheels in top condition. Here’s what you should be doing to ensure they last as long as possible:
How Often Should You Inspect Crane Wheels?
In high-use environments, crane wheels should be inspected at least once a month. Look for signs of wear, cracks, or other damage that could impact performance. Catching these issues early can save you from costly repairs later.
Best Practices for Crane Wheel Maintenance
Clean the wheels regularly, lubricate them as needed, and check for any signs of corrosion or wear. Maintaining proper track alignment is also essential to keep the wheels from wearing out prematurely.
Innovations in Crane Wheel Technology
The world of crane wheels is constantly evolving. Recent innovations are helping improve the performance and lifespan of these critical components. Let’s explore some of the latest developments.
Wear-Resistant Coatings
One of the most exciting innovations is the introduction of wear-resistant coatings. These coatings can significantly extend the life of crane wheels, especially in high-stress environments where wheels are prone to wearing out quickly.
Self-Lubricating Wheels
Another advancement is self-lubricating wheels, which help reduce friction and wear over time. This technology minimizes the need for manual lubrication, cutting down on maintenance costs and downtime.
How to Choose the Right Crane Wheel Manufacturer
When it comes to choosing a manufacturer for your crane wheels, quality should be your top priority. Here’s what to look for:
Key Qualities to Look For
A good manufacturer will have a strong reputation for producing durable, high-quality wheels. Look for companies that use top-grade materials and have a proven track record in the industry.
Industry Certifications
Certifications can give you peace of mind that the manufacturer adheres to industry standards for safety and quality. Look for ISO or other relevant certifications when choosing a supplier.
Conclusion: Crane Wheels Are Critical for Heavy Lifting
At the end of the day, crane wheels are a small yet essential part of any lifting operation. From safety to productivity, choosing the right wheels can make or break your crane’s performance. Understanding the different types, materials, and key considerations can help you make informed decisions, ensuring your operations run smoothly and safely. So next time you’re thinking about crane maintenance, don’t forget to give those wheels the attention they deserve!
FAQs
Do crane wheels need lubrication?
Yes, many crane wheels require regular lubrication to reduce friction and wear, although some new technologies like self-lubricating wheels are now available.
How often should crane wheels be replaced?
Crane wheels should be replaced as soon as you notice signs of excessive wear or damage. Regular inspections will help you catch these signs early.
Can I use the same crane wheels indoors and outdoors?
Not necessarily. Environmental factors like moisture or extreme temperatures can impact wheel performance. Choose the right material based on where your crane operates.
What’s the difference between forged and cast crane wheels?
Forged wheels are generally stronger and more durable, making them ideal for heavy-duty applications, while cast wheels are more affordable and suitable for lighter loads.
How can I prevent crane wheel misalignment?
Regularly inspect the alignment of your crane’s track and wheels, and adjust as necessary to ensure smooth operation.
If you need any other crane kits,welcome to send a free inquiry.Email:info@kcicranes.com
Address
Xinxiang City, Henan Province, China
Phone & Whatsapp
+86 16650373589
info@kcicranes.com