KCICRANES-Professional Crane Kits Supplier
In the realm of industrial lifting apparatus, crane wheels are indispensable components, ensuring the seamless operation of heavy-duty machinery. As diverse industries demand tailored functionality, gaining insight into the different types of crane wheels is paramount. This article thoroughly examines the various crane wheel types, their constituent materials, manufacturing nuances, and their impact on operational efficiency and performance.
The Importance of Crane Wheel Selection
Crane wheels are engineered to bear the immense weight of cranes, enabling them to traverse beams or tracks effortlessly. Each variant of crane wheel is meticulously crafted to meet the distinct needs of specific operational environments. Hence, understanding the nuances of these wheels is essential for companies to make well-informed decisions when choosing the optimal wheel for their machinery.
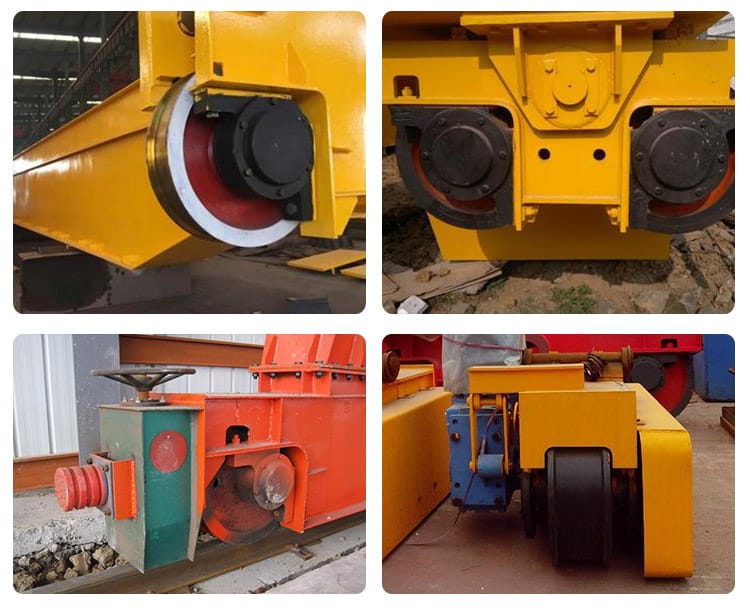
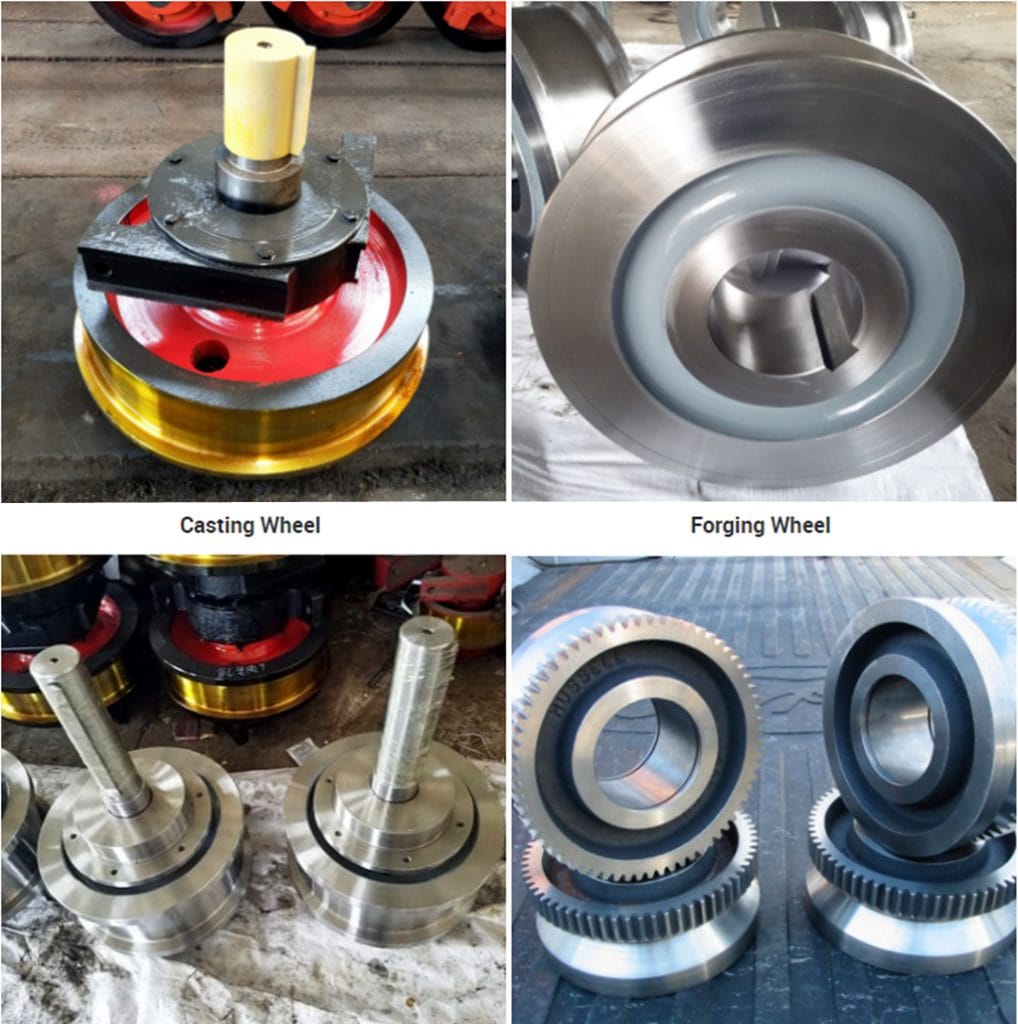
An Overview of Crane Wheel Types
Steel Crane Wheels
Overview: Steel wheels dominate in heavy-duty applications due to their ability to handle substantial loads. Their robust construction and inherent durability make them a preferred choice for demanding environments.
Applications: Commonly used in overhead cranes, gantry cranes, and a range of other lifting machinery requiring significant strength.
Aluminum Crane Wheels
Overview: Lightweight and resistant to corrosion, aluminum crane wheels offer a distinct advantage where weight reduction is crucial. These wheels are designed for mobility and quick maneuvering.
Applications: Predominantly used in portable crane systems and applications that prioritize weight and ease of transport.
Cast Iron Crane Wheels
Overview: Cast iron wheels blend formidable strength with superior wear resistance, providing a reliable solution for environments where frequent, heavy load handling is required.
Applications: Ideal for industrial settings characterized by rigorous demands and the frequent handling of substantial weight.
Key Factors in Crane Wheel Selection
The process of choosing the most appropriate crane wheel involves several pivotal considerations:
- Load Bearing Capacity
Each crane wheel is designed to withstand specific load thresholds. For instance, steel wheels excel in handling heavy loads, while aluminum wheels cater to lighter lifting requirements. - Material Composition
The choice of material is pivotal in determining a wheel’s performance. Steel is favored for its resilience and durability, while aluminum’s lightweight properties are indispensable in certain specialized applications. - Operational Environment
The environment in which the crane will operate is another critical factor. Steel wheels are ideal for rugged, outdoor conditions, offering resilience against harsh weather, while aluminum wheels are best suited for indoor or portable systems, where corrosion resistance and reduced weight are paramount. - Wheel Design
The design—ranging from the tread pattern to the overall dimensions—plays a significant role in the performance of crane wheels. Some are crafted with specific tread patterns to optimize grip, while others prioritize smooth, swift movement, thus influencing the overall operational fluidity.
The Intricate Process of Crane Wheel Manufacturing
The production of crane wheels involves multiple stages, each crucial in ensuring the final product meets stringent standards:
- Material Selection
The initial step in manufacturing crane wheels involves sourcing materials based on the specific requirements of the wheel type. Steel and aluminum are the two primary materials, each chosen for their respective mechanical properties. - Design & Engineering
Using cutting-edge CAD software, skilled engineers create precise designs for each wheel type. This phase encompasses detailed considerations of dimensions, weight tolerance, and specific features necessary for the wheel’s intended function. - Machining
In this phase, raw materials are shaped and cut with high precision to form the components of the crane wheels. The accuracy of this process is vital for ensuring each wheel meets the exact specifications. - Heat Treatment
For steel wheels, heat treatment techniques such as quenching and tempering are applied. These processes enhance the hardness of the steel, thereby boosting the wheel’s capacity to endure heavy-duty conditions. - Assembly
Once the individual components are ready, the wheels are assembled, with bearings and seals fitted as required. This phase ensures the smooth functionality and durability of the wheels. - Quality Control
Quality control is an essential aspect of crane wheel manufacturing. Every batch undergoes stringent testing protocols, including load-bearing tests and dimensional accuracy checks, ensuring the product meets safety and operational standards. - Surface Finishing
The final stage involves applying surface treatments, such as coatings or paints, which enhance the corrosion resistance and aesthetics of the wheels, ultimately contributing to their longevity.
The Advantage of Comprehending Crane Wheel Types
A profound understanding of the various crane wheel types and their specific uses confers several distinct benefits:
- Augmented Safety
Choosing the correct crane wheel type significantly mitigates the risk of operational failures or accidents. Properly designed wheels enhance stability and control, particularly in critical lifting applications. - Enhanced Efficiency
The selection of the right wheels ensures smooth, frictionless movement, thereby boosting operational efficiency. By reducing wear and tear, the need for energy consumption diminishes, leading to long-term cost savings. - Longevity & Durability
Quality crane wheels made from the appropriate materials are capable of enduring harsh conditions, offering extended service life and reduced maintenance demands. - Tailored Solutions
Companies like KCICRANES Machinery provide customization options for crane wheels, enabling clients to acquire products finely tuned to their specific operational needs.
KCICRANES Machinery: Your Expert Partner in Crane Wheel Solutions
At KCICRANES Machinery, a premier crane manufacturer headquartered in China, we specialize in a broad spectrum of high-quality lifting equipment. Our portfolio includes:
- Overhead Cranes
- Portable Gantry Cranes
- Crane Wheels
- Crane Beams
- Grab Buckets
- Crane Winches
- Electric Hoists
We are committed to ensuring excellence in both the products we produce and the service we provide. Our advanced manufacturing techniques and rigorous quality control ensure that each crane wheel we produce adheres to the highest industry standards.
Why Trust KCICRANES for Your Crane Wheel Needs?
- Expertise: With years of experience in crane manufacturing, our team possesses the deep technical knowledge needed to produce the finest crane wheels.
- Customization: We offer bespoke solutions, adapting our products to suit your precise operational demands.
- Assured Quality: Each crane wheel undergoes thorough testing to meet performance and safety standards, providing clients with peace of mind.
- Competitive Pricing: We deliver superior crane wheels at competitive prices, ensuring optimal value for your investment.
- Enduring Support: From your first inquiry to ongoing post-purchase assistance, we stand by you at every stage.
Frequently Asked Questions About Crane Wheel Types
- What are the main types of crane wheels available?
The primary types include steel, aluminum, and cast iron crane wheels, each designed for distinct load-bearing capacities and operational environments. - How do I choose the right crane wheel for my needs?
Consider the load capacity, operating conditions, and the specific requirements of your crane system to make an informed decision. - Can crane wheels be customized?
Yes, many manufacturers, including KCICRANES, offer customized options to meet your unique requirements. - What is the typical lifespan of crane wheels?
The lifespan varies based on material and application, but high-quality wheels can last for many years with proper maintenance. - How can I ensure the quality of crane wheels?
Select a reputable manufacturer known for its stringent quality control measures and robust product warranties.
Embracing the Future of Crane Wheel Technology
As modern industries’ demands evolve, so will the need for specialized crane wheels. Gaining a deeper understanding of the available options empowers businesses to make decisions that enhance safety, operational efficiency, and durability. At KCICRANES Machinery, we are dedicated to providing cutting-edge crane wheel solutions that address the evolving needs of our clients. Whether you require standard or bespoke solutions, our expertise ensures you receive the best products tailored to your operational demands.
For more details or to request a consultation, please get in touch with us at info@kcicranes.com.
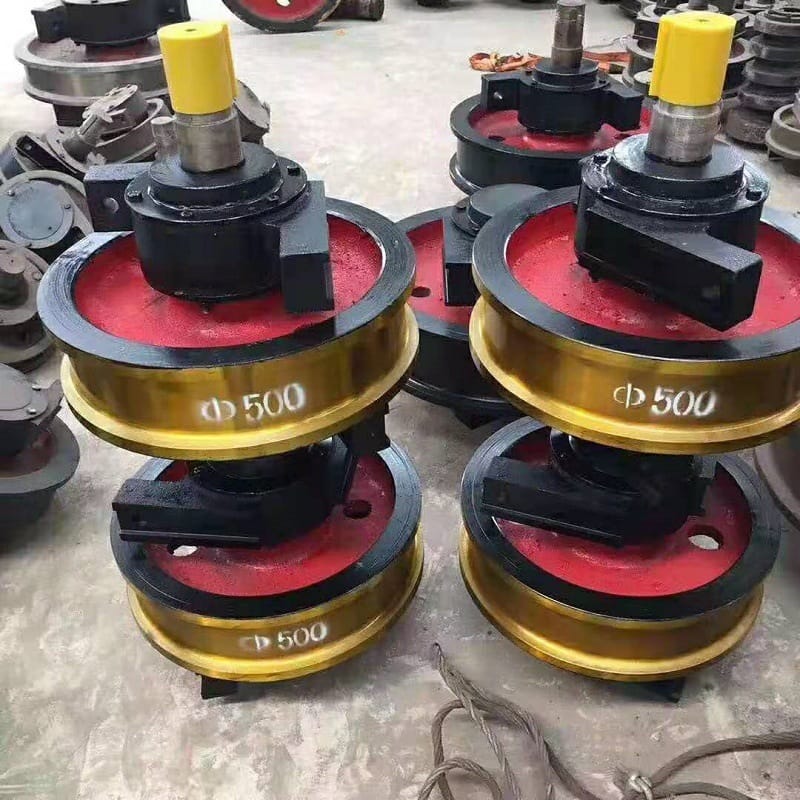
Parameter | Range |
Wheel Materials | 42CrMo,60Mn,65Mn,55#,60#,ZG340-640 .etc |
Manufacturing Process | Forging,Casting,Rollmilling .etc |
Wheel Diameter/mm | 200,250,315,400,500,630,710,800,1000 .etc |
Wheel Gross Weight/kg | 82-87kg;133-163kg;200-262kg;284-405kg;605-1000kg .etc |
Lifting Speed | 3 to 12 m/min |
General bearing force | 8-104 Tons |
Applications | Overhead cranes,gantry cranes,transfer carts,trains.etc |
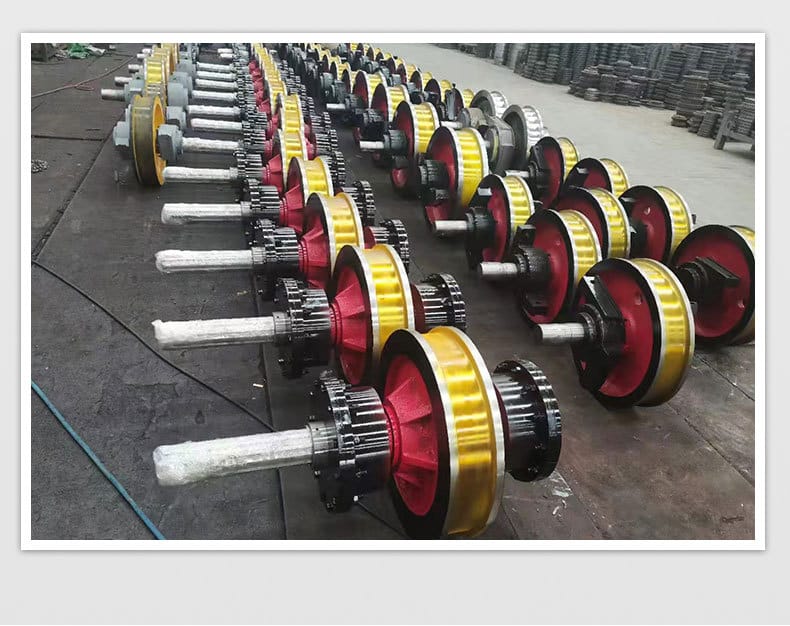
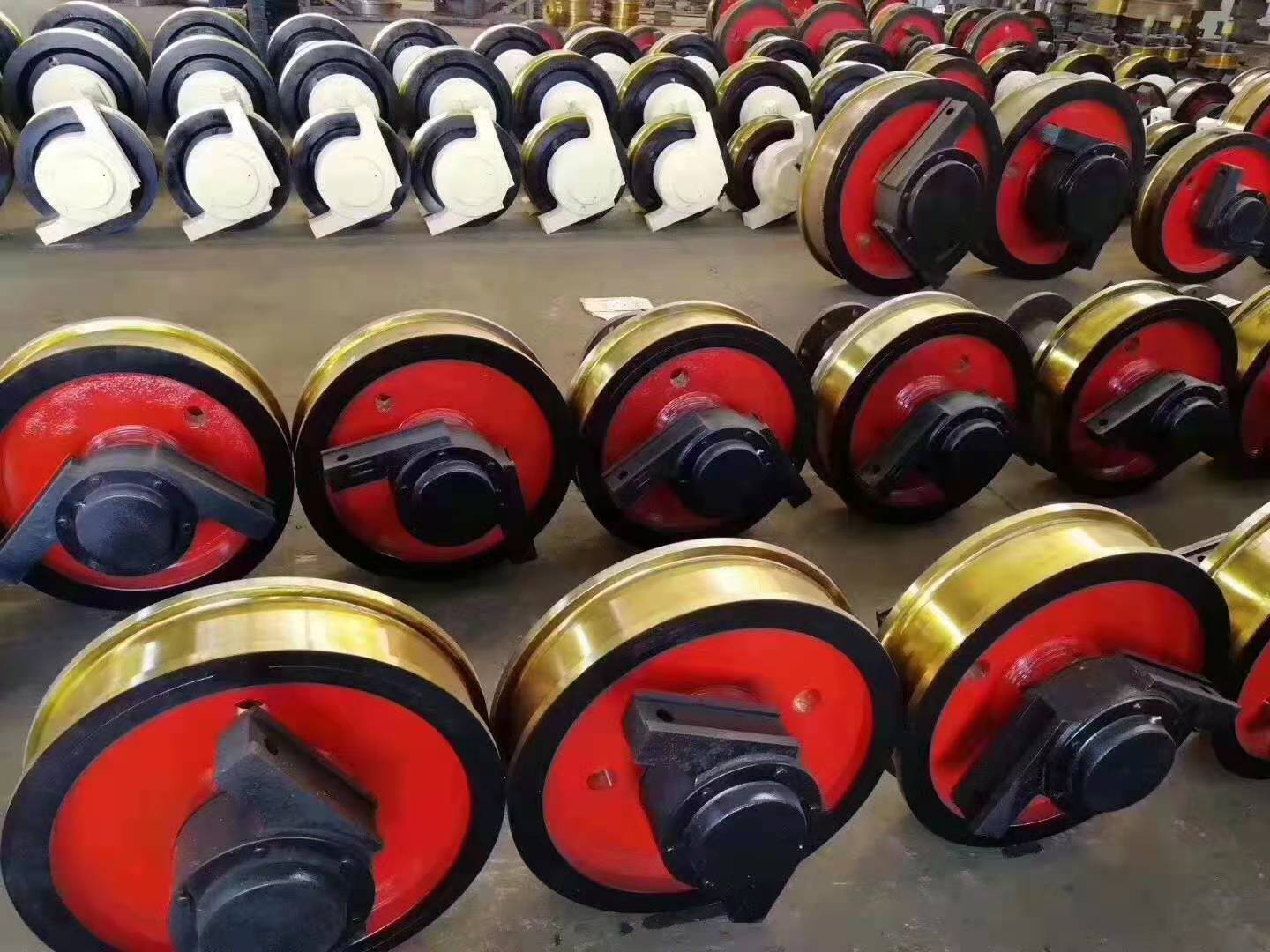

Parameter | Range |
Loading Capacity | 2 to 100 tons |
Wheel Diameter | Φ200mm-Φ800mm |
Wheel Gross Weight/kg | 80-500kg |
DRS gearbox | Drive Reduction System |
Drive Control | Allows for precise control of the crane’s movement speed and direction |
Durability | Typically made from high-strength materials to withstand harsh working environments. |
Control Method | Remote control, Pendant control, or Cabin control |
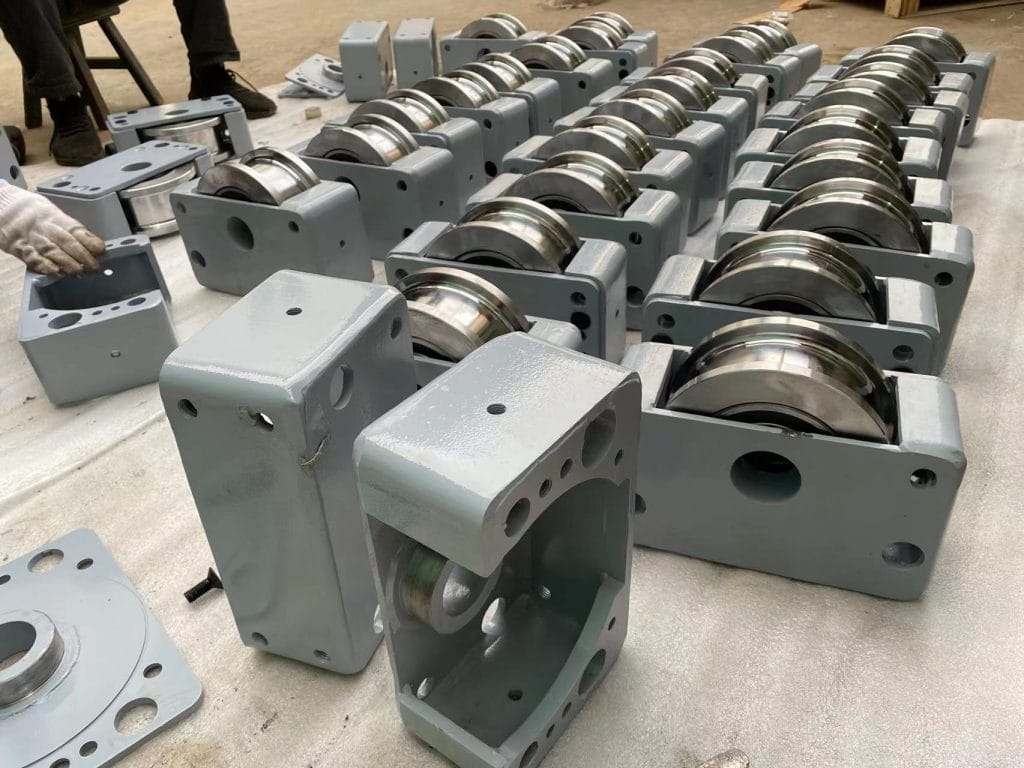
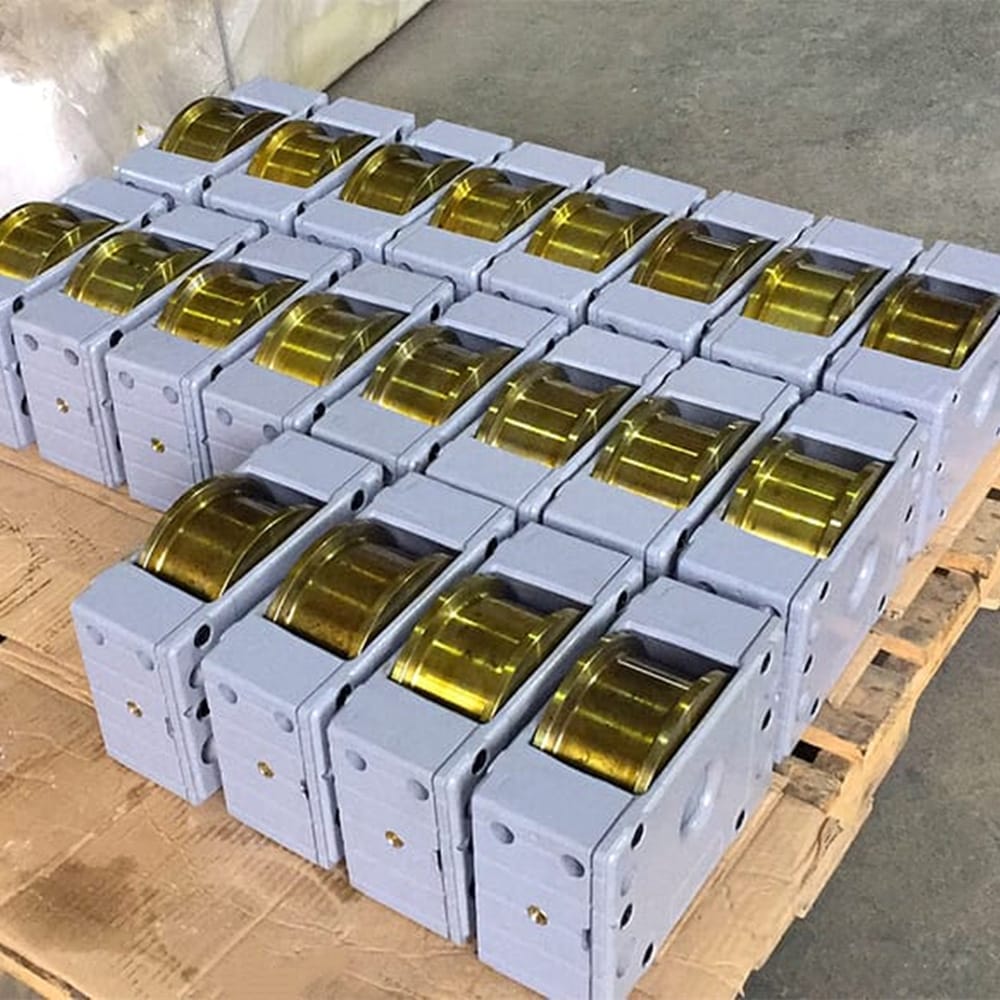
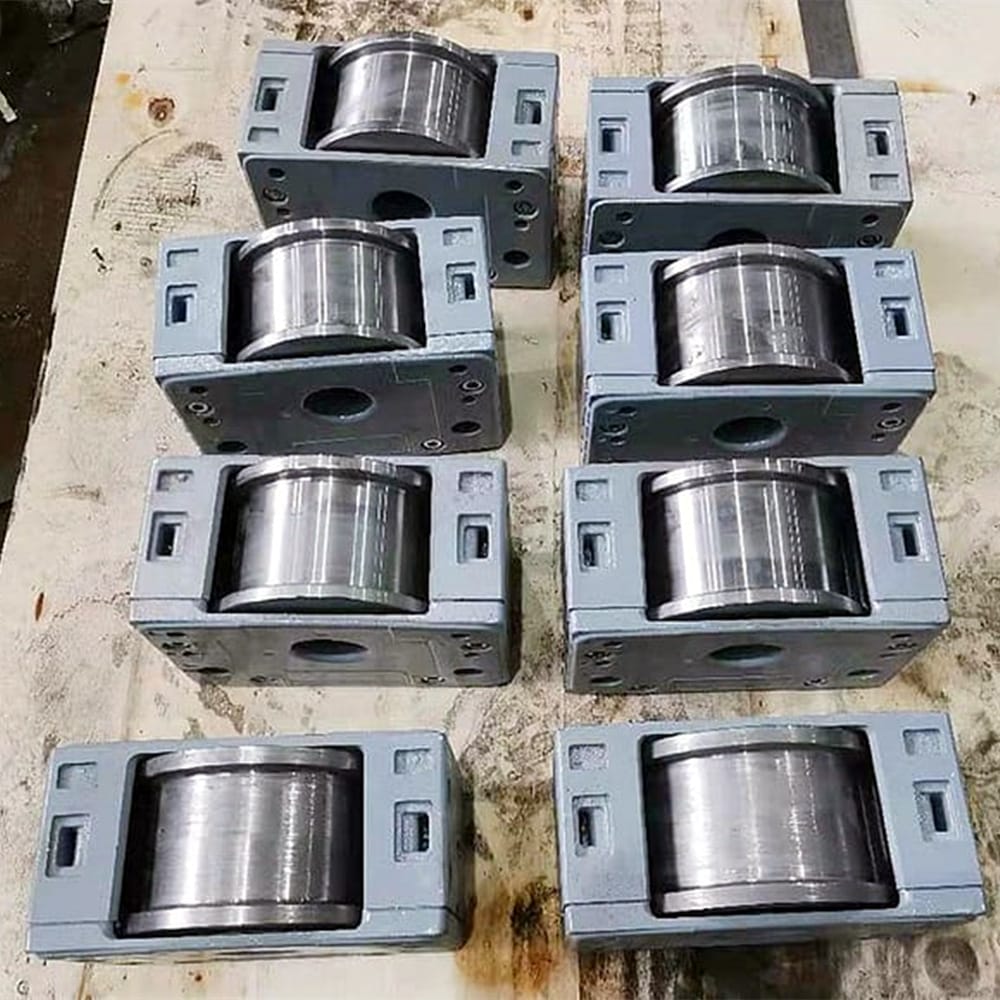
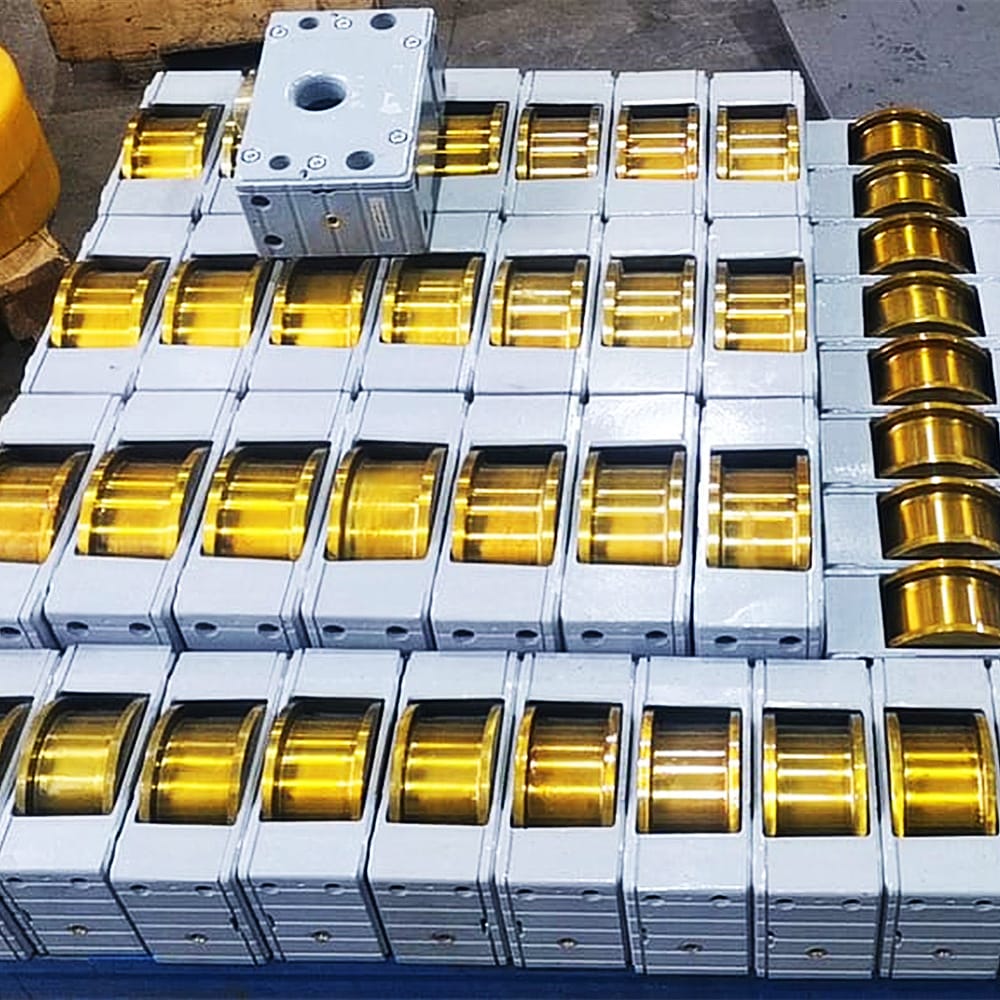
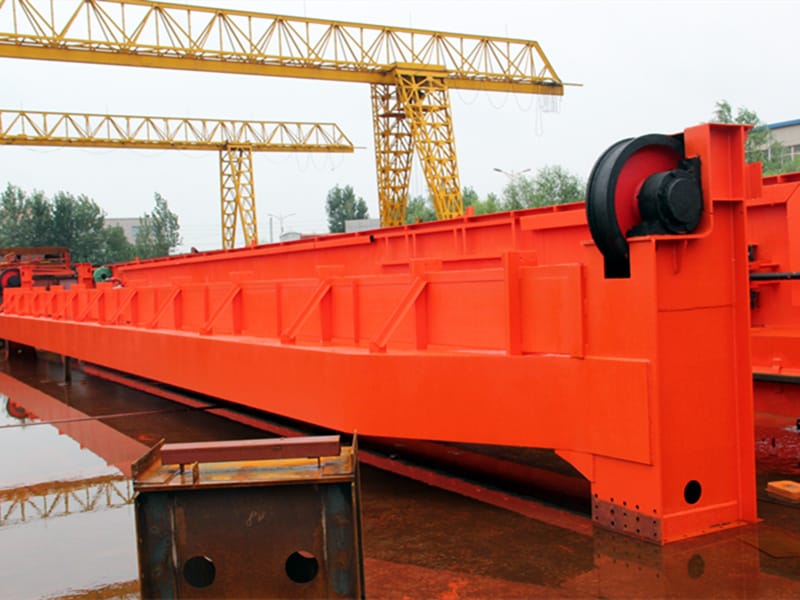
Parameter | Range |
Lifting Capacity | 250kg to 120 tons |
Wheel Diameter | Φ200mm-Φ800mm |
Wheel Gross Weight/kg | 80-500kg |
Thickness | Typically range from 50 mm to 200 mm |
Wheel Type | Solid wheels, grooved wheels, flanged wheels.etc |
Operating Temperature | From -20°C to +100°C |
Materials | Stainless steel, alloy steel, and cast iron.etc |
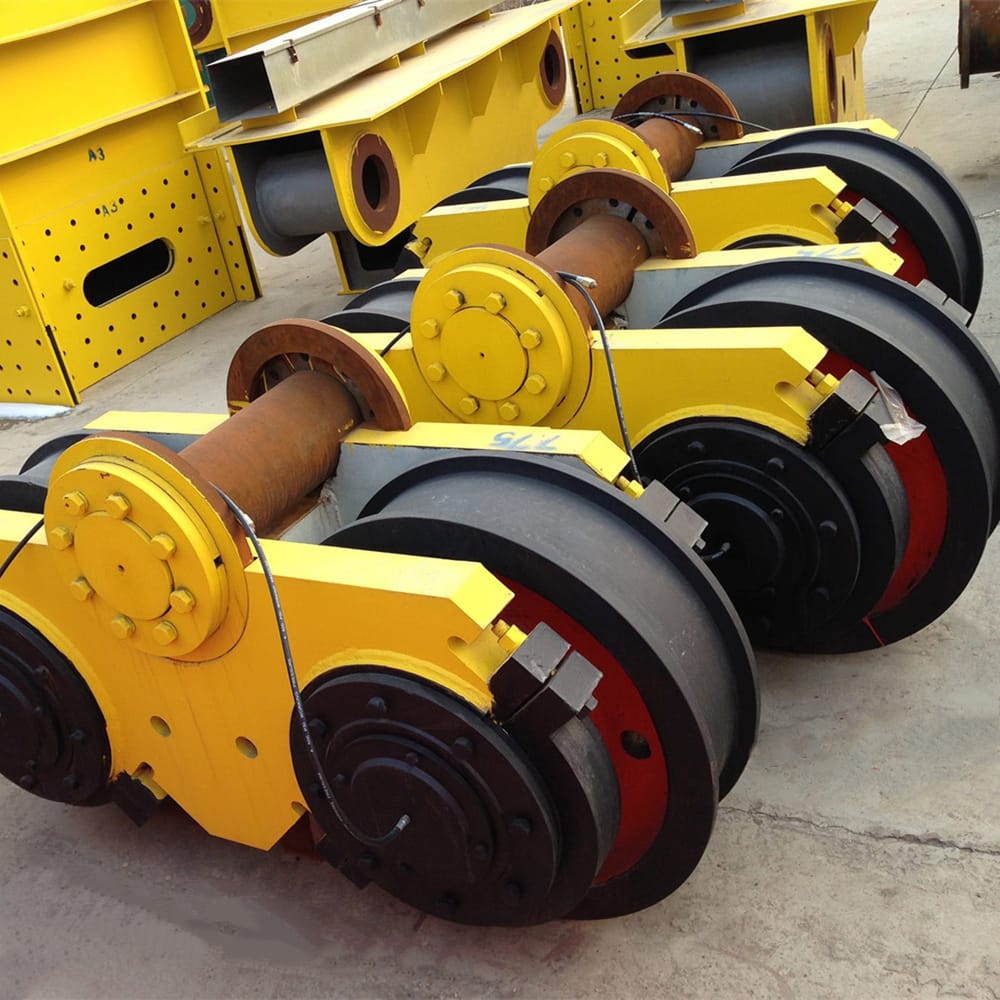
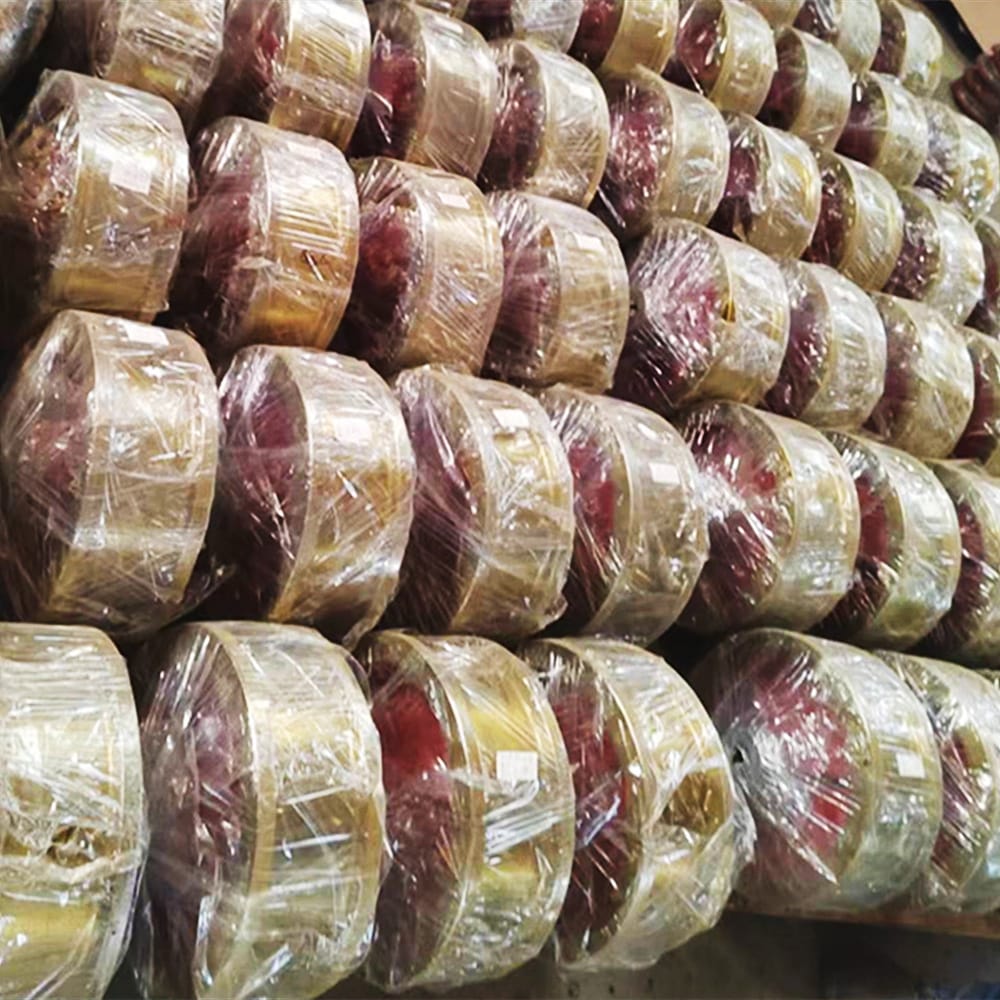
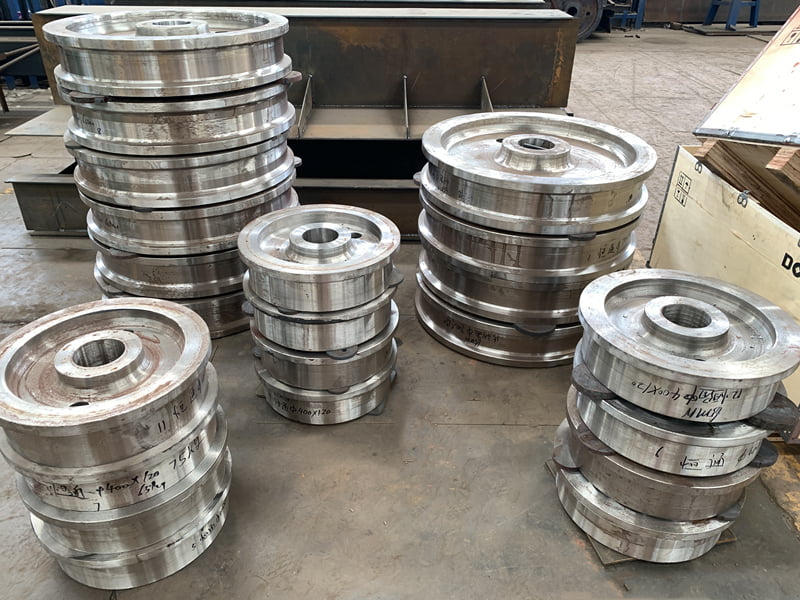
Address
Xinxiang City, Henan Province, China
Phone & Whatsapp
+86 16650373589
info@kcicranes.com