KCICRANES-Professional Crane Kits Supplier
Crane wheels play a critical role in the efficient and safe operation of industrial cranes. Among the different types available, forged crane wheels and cast crane wheels are the most popular. But which one should you choose for your project? This article will break down their differences, including material composition, production methods, and applications, to help you make an informed decision.
At KCICRANES Machinery, a leading crane and crane parts manufacturer in China, we specialize in high-quality crane solutions. For inquiries, contact us at info@kcicranes.com.
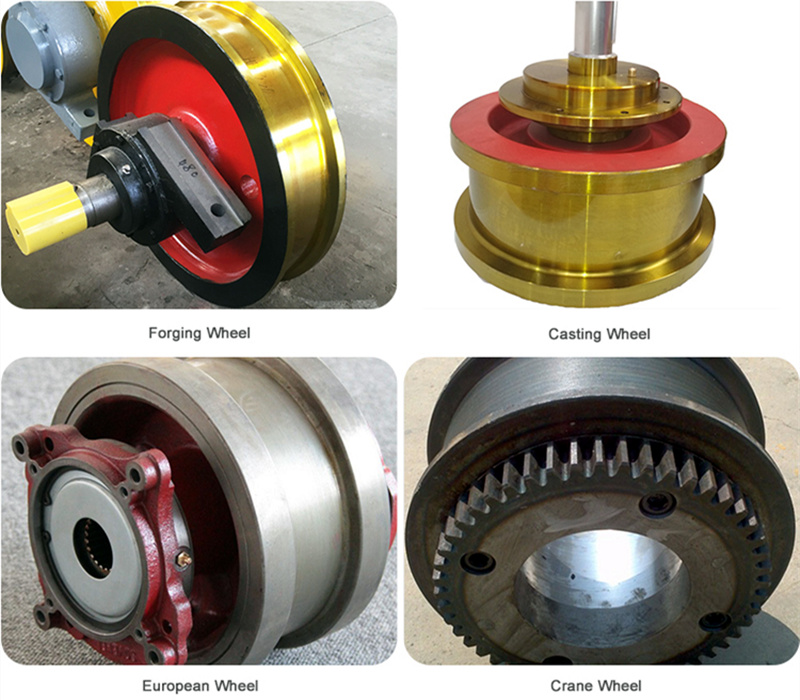
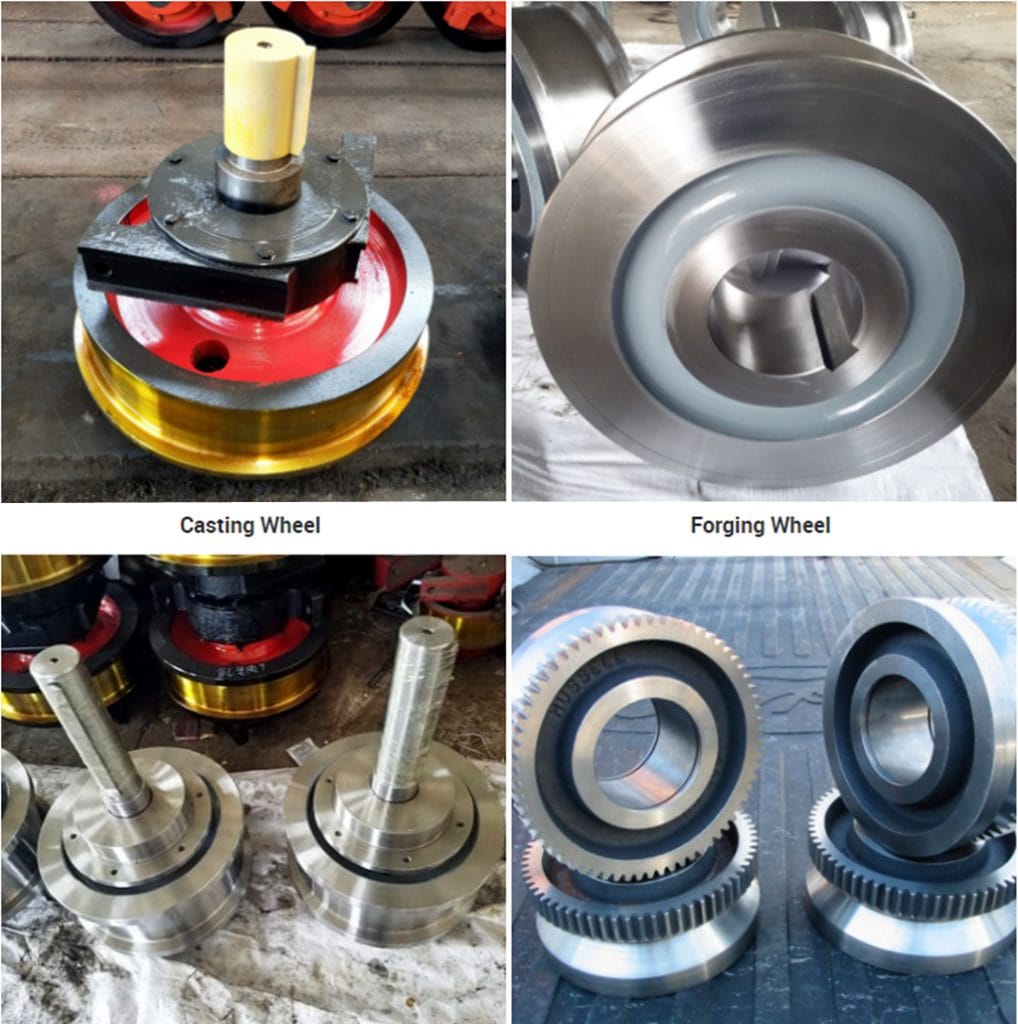
Material Composition
Forged Crane Wheels:
Forged wheels are made from high-quality steel or steel alloys. The forging process compresses the metal, eliminating voids and creating a denser, stronger structure. This makes forged wheels highly resistant to cracking, fatigue, and deformation.
Cast Crane Wheels:
Cast wheels are produced by pouring molten metal, typically cast iron or steel, into molds. While cast iron offers good wear resistance, cast wheels tend to have internal voids or inconsistencies, which can weaken their structure over time.
Key Difference:
Forged wheels are denser and more durable due to their refined grain structure, whereas cast wheels are more cost-effective but may lack the same level of strength.
Production Process
Forged Crane Wheels:
The forging process involves heating a steel billet and shaping it under high pressure using a die. This method creates a uniform grain flow, improving the wheel’s strength and resistance to stress.
Cast Crane Wheels:
In casting, molten metal is poured into a mold and left to cool. Once solidified, the wheel is machined to achieve the desired dimensions. Casting allows for complex shapes but may introduce defects like porosity.
Key Difference:
Forging produces wheels with superior mechanical properties, while casting is better for manufacturing intricate designs at a lower cost.
Strength and Durability
Forged Crane Wheels:
Thanks to their dense structure, forged wheels can withstand heavy loads and high-impact environments. They are less likely to chip or crack, even under extreme conditions.
Cast Crane Wheels:
Cast wheels are generally less robust. They may wear out faster or develop cracks when subjected to high stress.
Key Difference:
For applications requiring high strength and long service life, forged wheels are the better choice. Cast wheels are suitable for lighter loads and less demanding conditions.
Precision and Surface Finish
Forged Crane Wheels:
Forging ensures precise dimensions and a smoother surface finish. This precision reduces friction during operation, improving the overall efficiency of the crane.
Cast Crane Wheels:
Cast wheels may have slight inconsistencies in their surface finish due to the molding process. These imperfections can increase wear and friction over time.
Key Difference:
Forged wheels offer better precision and performance compared to cast wheels.
Applications
Forged Crane Wheels:
- Heavy-duty applications, such as gantry cranes, overhead cranes, and mining equipment.
- Industries requiring durability and reliability, including steel production, shipbuilding, and construction.
- Environments with high stress and harsh conditions.
Cast Crane Wheels:
- Light-duty cranes or applications where cost is a major consideration.
- Situations where custom shapes or designs are required.
Key Difference:
Forged wheels dominate heavy industries, while cast wheels are more common in lighter, less demanding applications.
Cost Considerations
Forged Crane Wheels:
The production of forged wheels is labor-intensive and requires specialized equipment. This makes them more expensive than cast wheels.
Cast Crane Wheels:
Casting is a simpler process and, therefore, more economical. However, the lower upfront cost may be offset by higher maintenance or replacement costs over time.
Key Difference:
Forged wheels are an investment in long-term reliability, while cast wheels offer a budget-friendly option for less critical tasks.
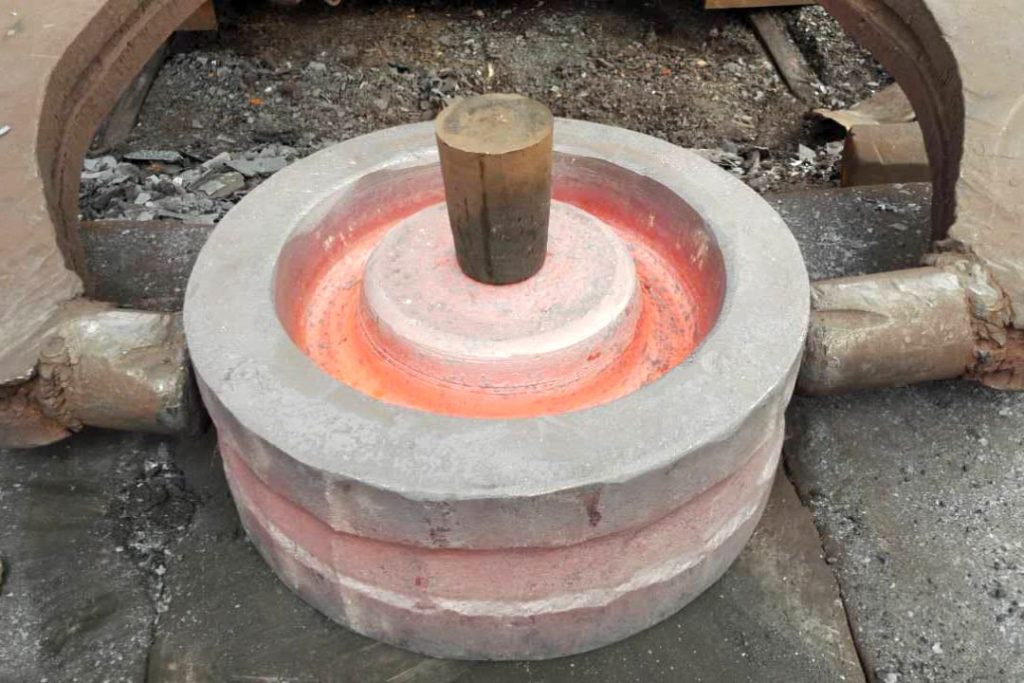
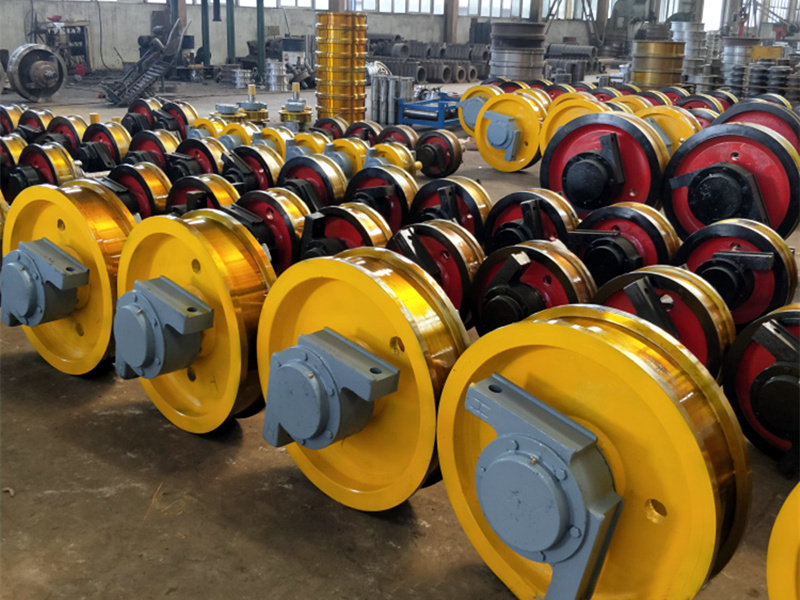
Choosing the Right Crane Wheel
When deciding between forged and cast crane wheels, consider the following:
- Load Requirements: For heavy-duty tasks, forged wheels provide unmatched strength and durability.
- Budget: If cost is a constraint and the application isn’t demanding, cast wheels can be a practical choice.
- Environment: For outdoor or high-stress environments, forged wheels are the safer, longer-lasting option.
- Maintenance: Forged wheels require less frequent replacement, reducing downtime and maintenance costs.
Why Choose KCICRANES Machinery?
At KCICRANES Machinery, we understand the importance of reliable crane components. Our forged crane wheels are manufactured to the highest standards, ensuring exceptional performance and longevity. Whether you need a standard design or a custom solution, we’ve got you covered.
Contact us at info@kcicranes.com for more information or to get a quote.
Conclusion
The choice between forged crane wheels and cast crane wheels depends on your specific needs. While cast wheels are more affordable, forged wheels offer superior strength, durability, and reliability. For industries requiring heavy-duty performance, forged crane wheels are the clear winner. At KCICRANES Machinery, we’re committed to providing the best solutions for your lifting needs.
Invest in quality, and let us help you lift your business to new heights!
FAQs
- What are the main advantages of forged crane wheels?
Forged crane wheels offer superior strength, durability, and resistance to wear and tear, making them ideal for heavy-duty applications. - Are cast crane wheels suitable for outdoor use?
While cast crane wheels can be used outdoors, they may not withstand extreme conditions as well as forged wheels. - How long do forged crane wheels last?
With proper maintenance, forged crane wheels can last for several years, even under heavy use. - Can KCICRANES Machinery customize crane wheels?
Yes, we provide tailored solutions to meet your specific requirements. - Which industries benefit most from forged crane wheels?
Industries like construction, steel production, mining, and shipbuilding rely heavily on forged crane wheels for their strength and reliability.
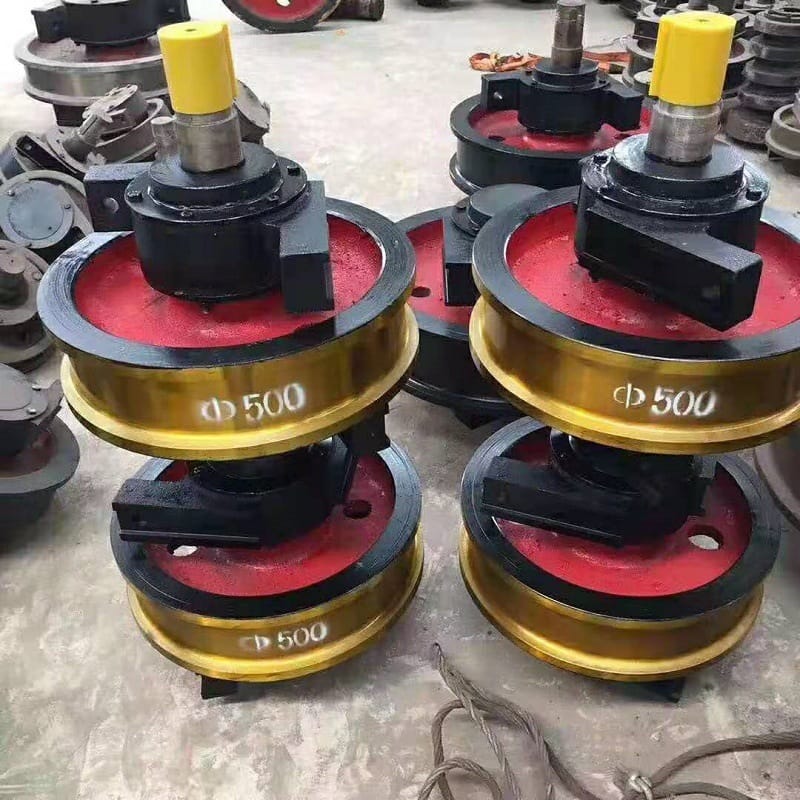
Parameter | Range |
Wheel Materials | 42CrMo,60Mn,65Mn,55#,60#,ZG340-640 .etc |
Manufacturing Process | Forging,Casting,Rollmilling .etc |
Wheel Diameter/mm | 200,250,315,400,500,630,710,800,1000 .etc |
Wheel Gross Weight/kg | 82-87kg;133-163kg;200-262kg;284-405kg;605-1000kg .etc |
Lifting Speed | 3 to 12 m/min |
General bearing force | 8-104 Tons |
Applications | Overhead cranes,gantry cranes,transfer carts,trains.etc |
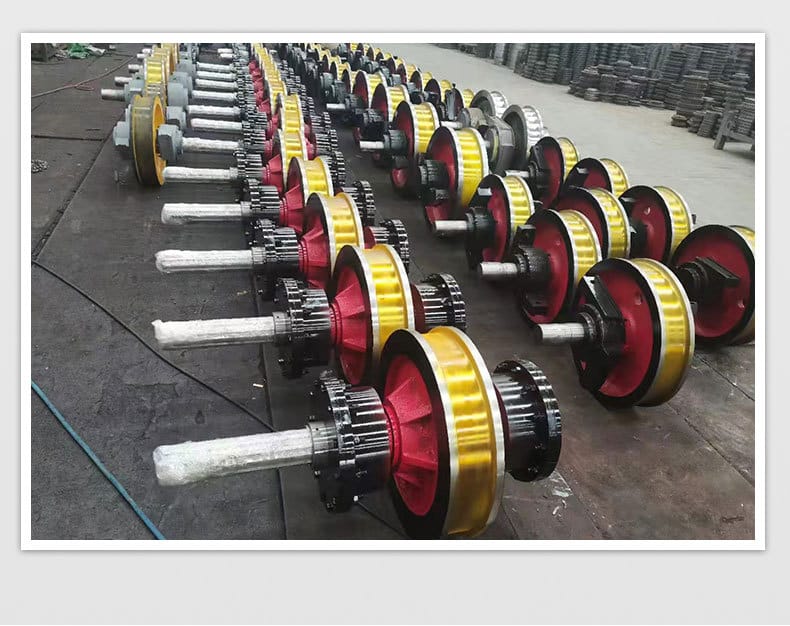
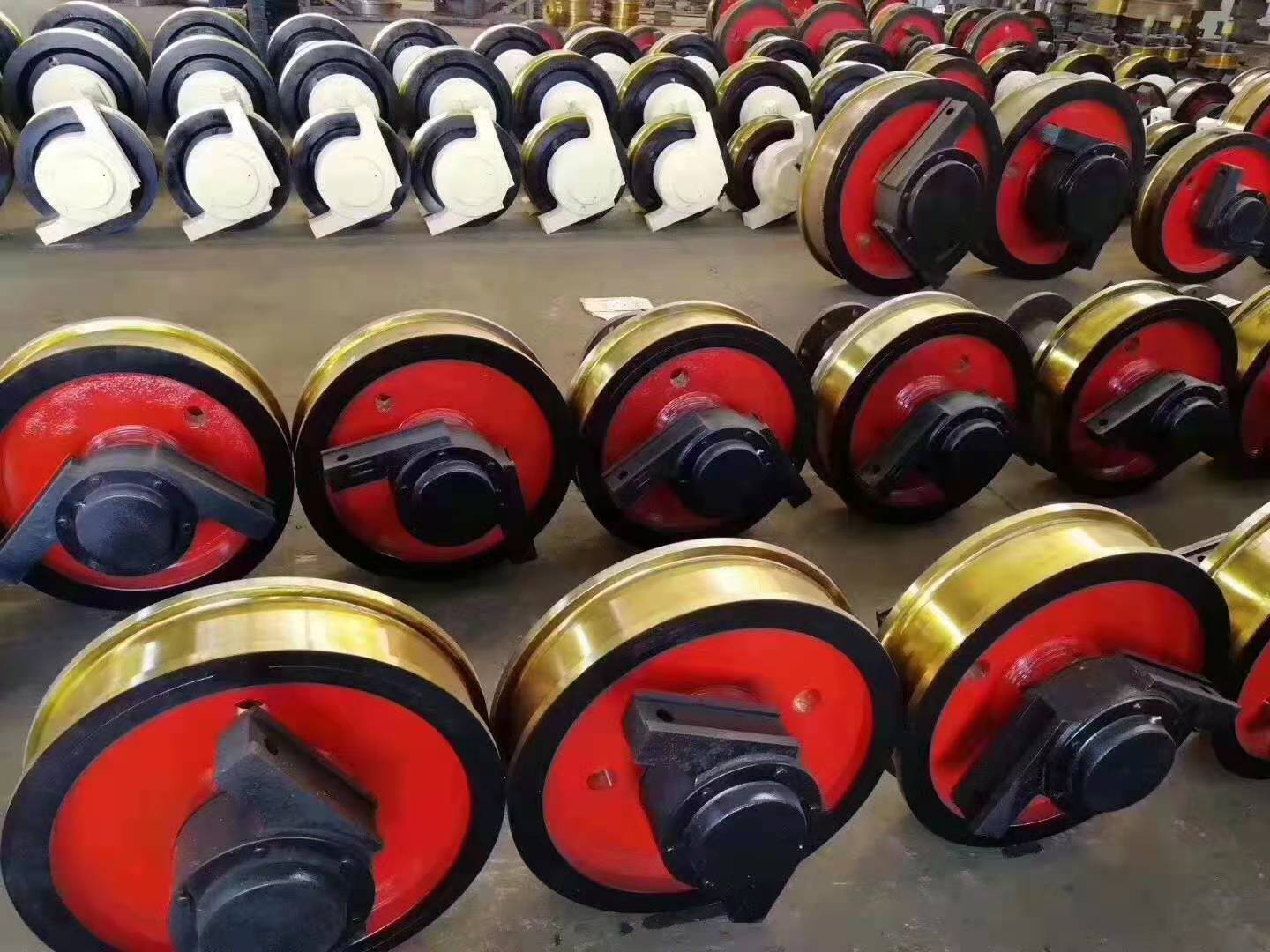

Parameter | Range |
Loading Capacity | 2 to 100 tons |
Wheel Diameter | Φ200mm-Φ800mm |
Wheel Gross Weight/kg | 80-500kg |
DRS gearbox | Drive Reduction System |
Drive Control | Allows for precise control of the crane’s movement speed and direction |
Durability | Typically made from high-strength materials to withstand harsh working environments. |
Control Method | Remote control, Pendant control, or Cabin control |
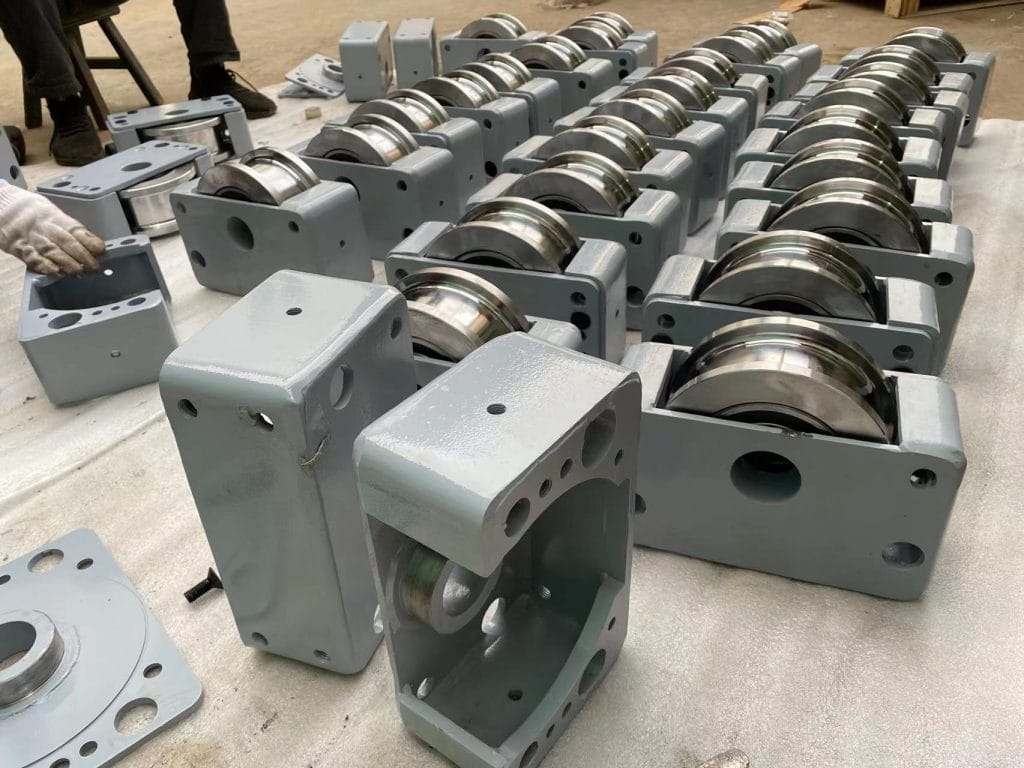
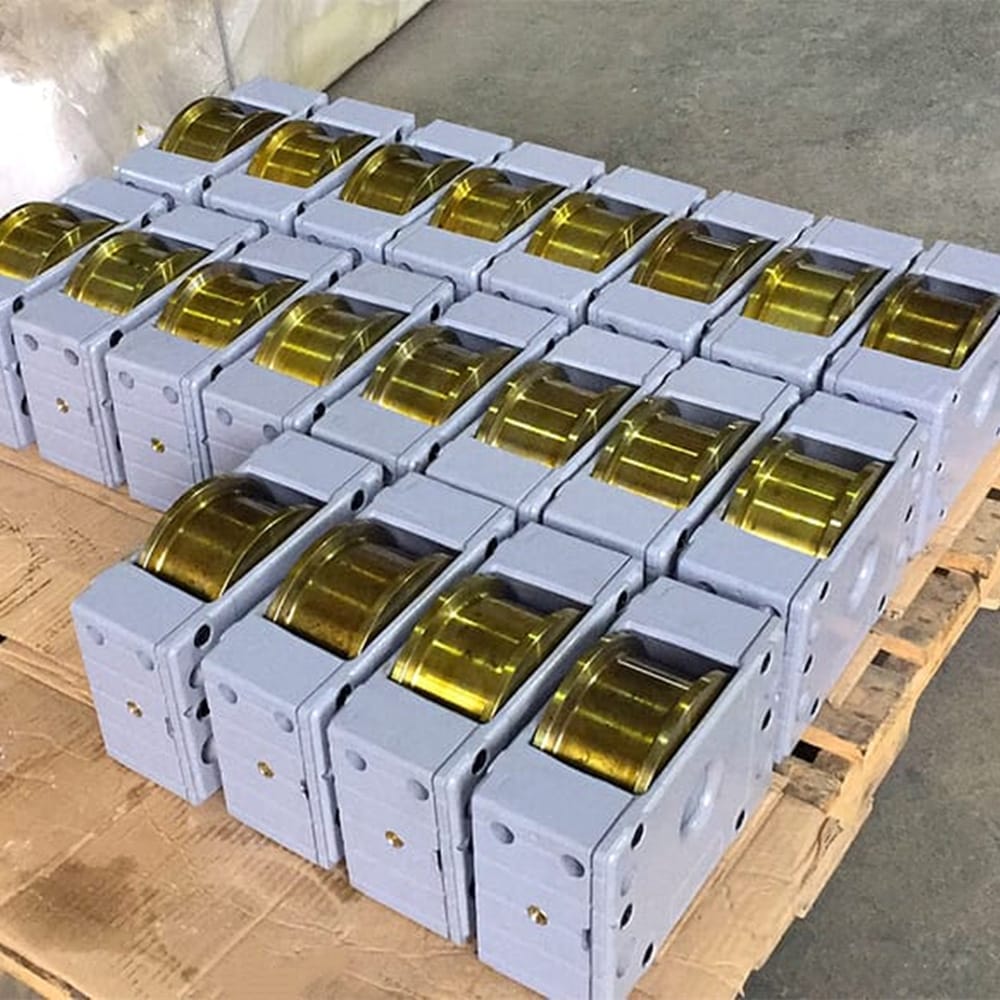
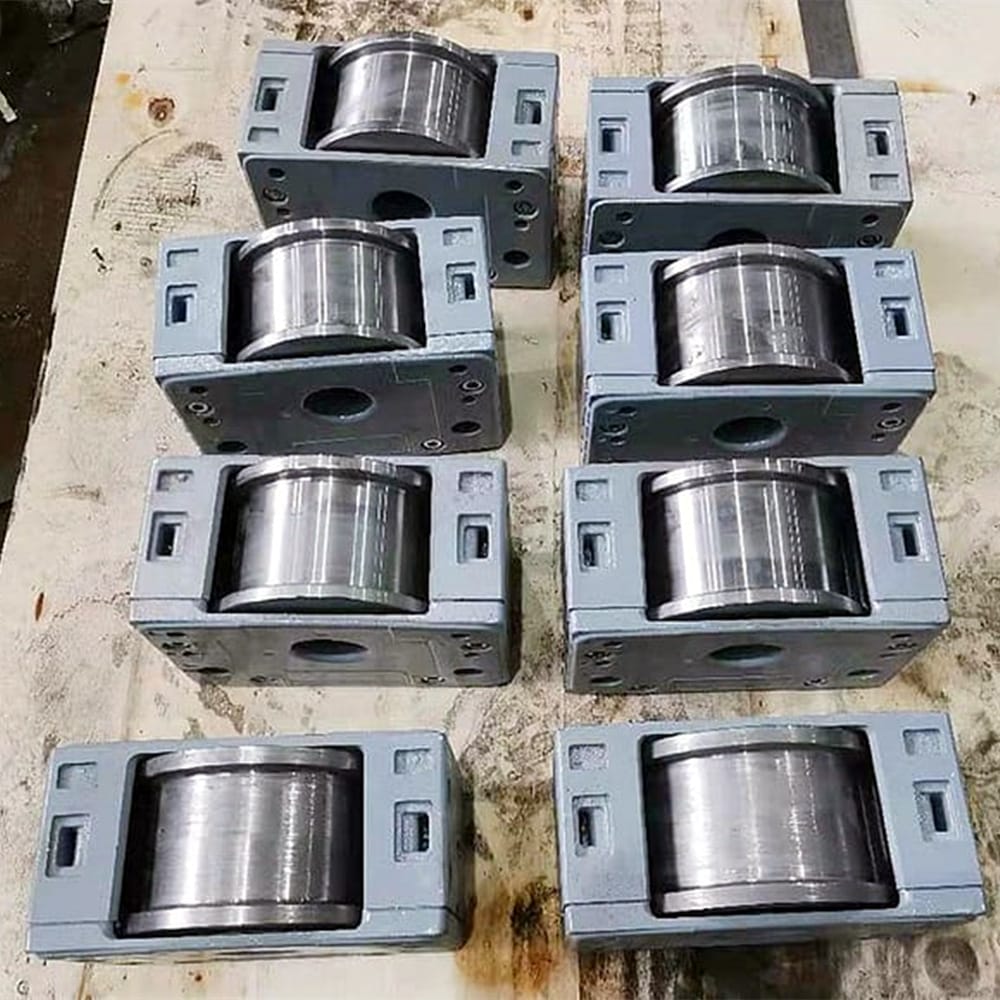
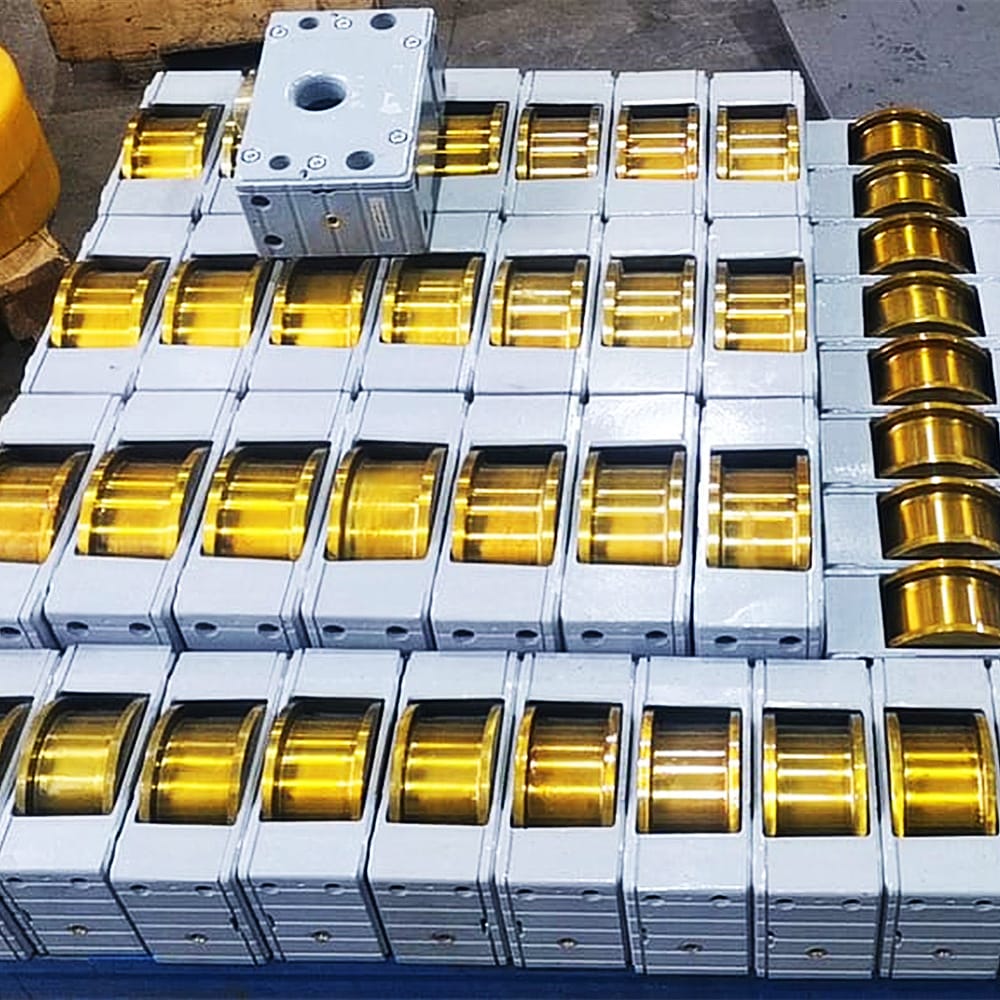
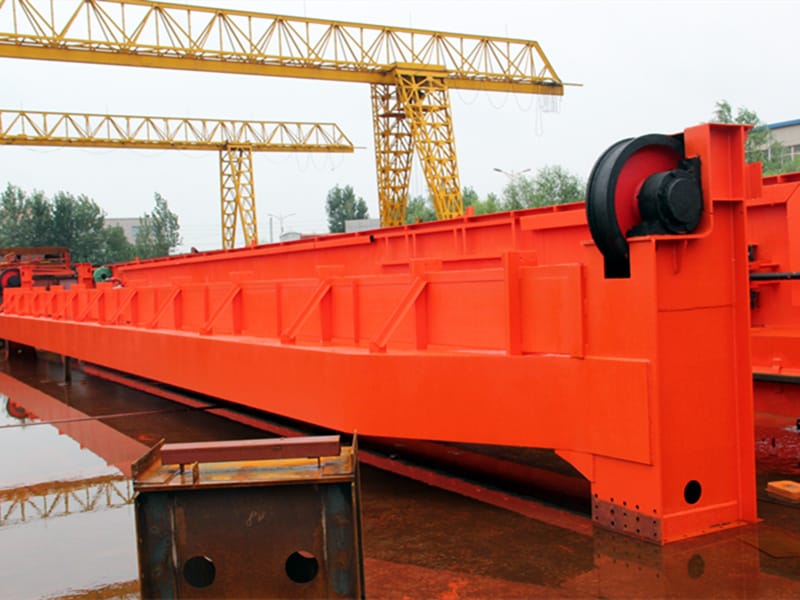
Parameter | Range |
Lifting Capacity | 250kg to 120 tons |
Wheel Diameter | Φ200mm-Φ800mm |
Wheel Gross Weight/kg | 80-500kg |
Thickness | Typically range from 50 mm to 200 mm |
Wheel Type | Solid wheels, grooved wheels, flanged wheels.etc |
Operating Temperature | From -20°C to +100°C |
Materials | Stainless steel, alloy steel, and cast iron.etc |
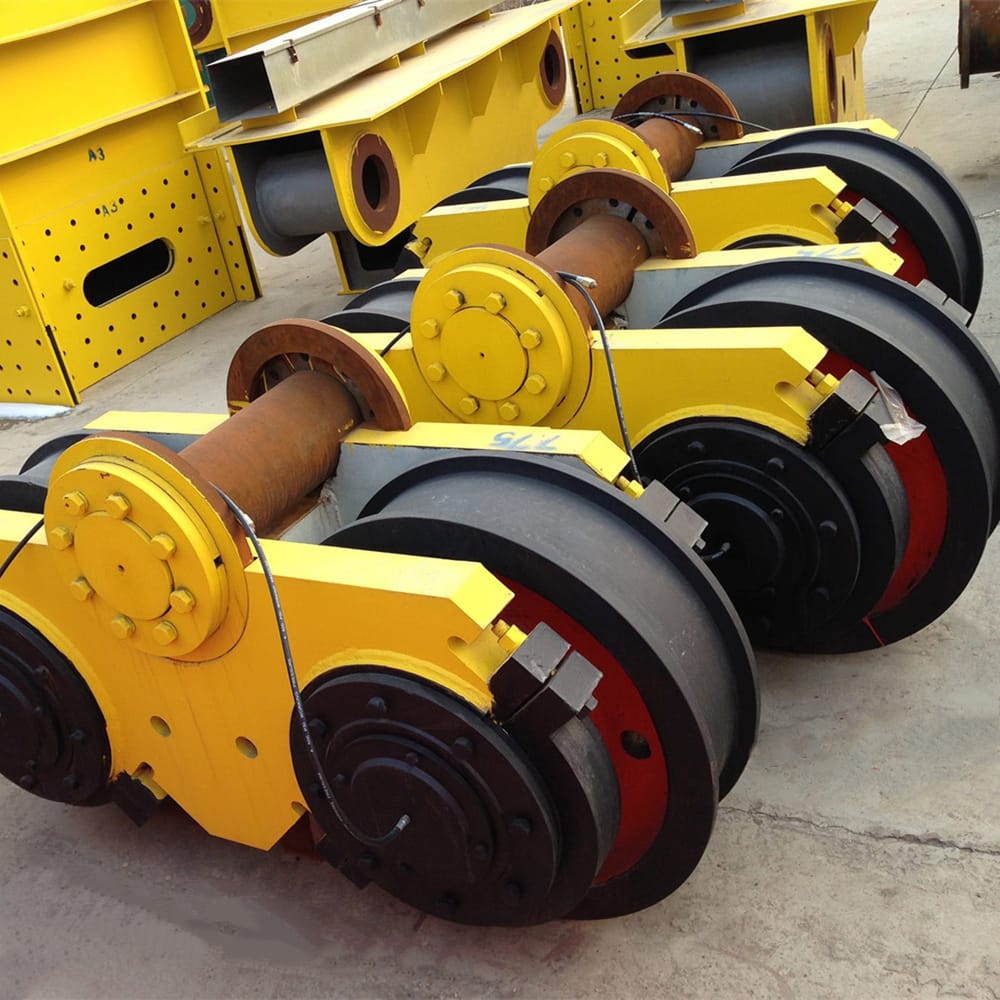
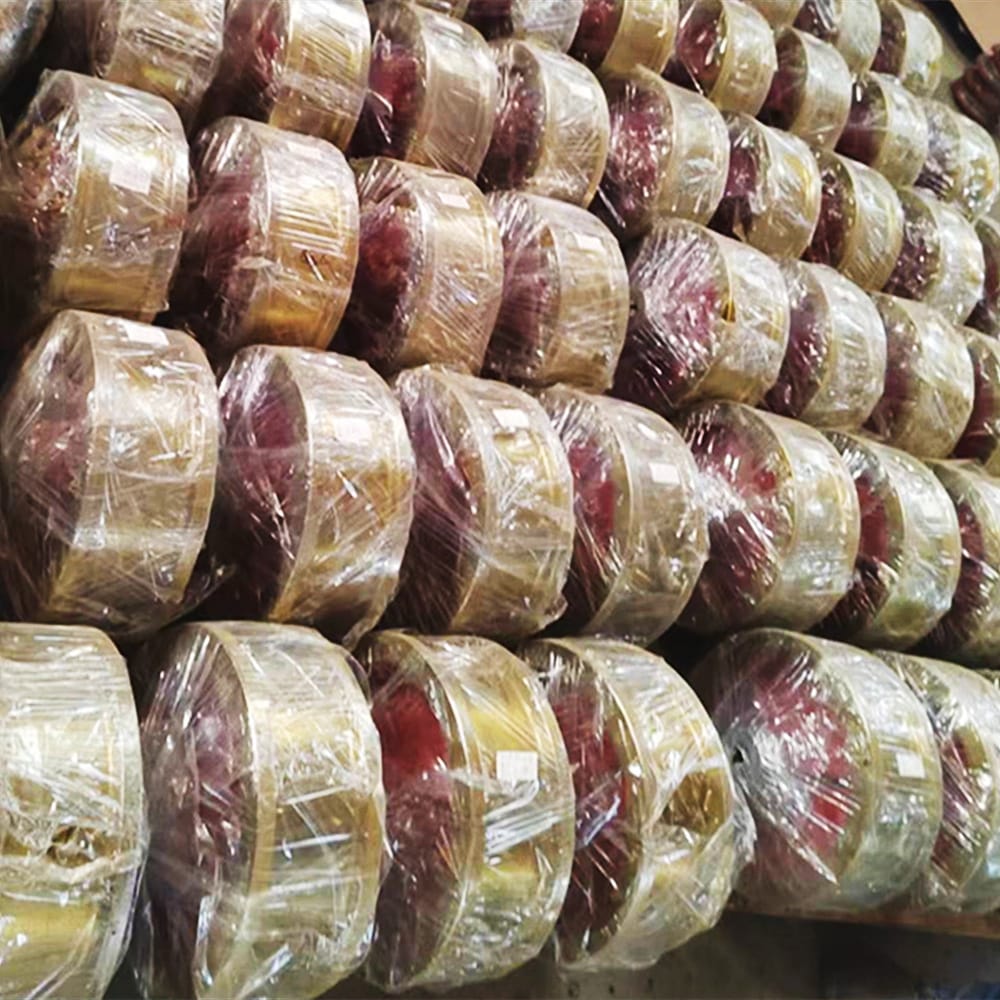
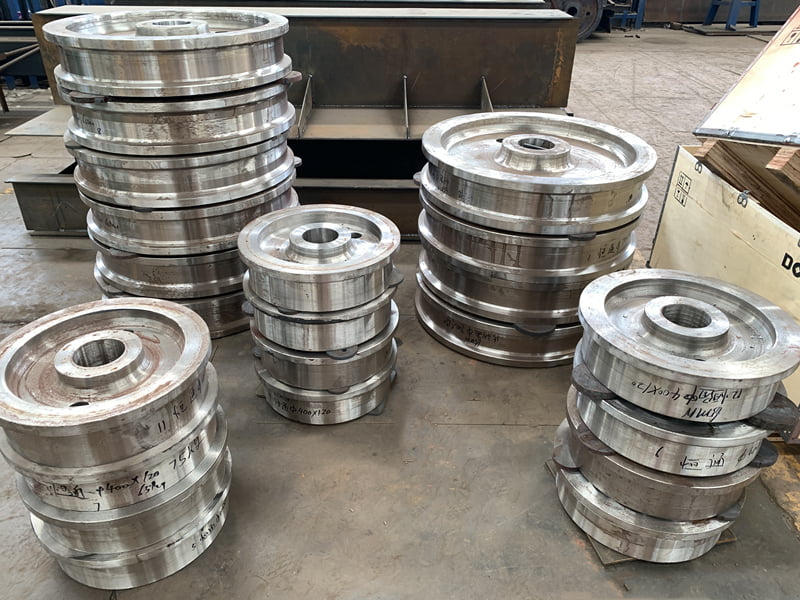
Address
Xinxiang City, Henan Province, China
Phone & Whatsapp
+86 16650373589
info@kcicranes.com